Maximum dimensions: Ø 800 mm x 2,000 mm depth
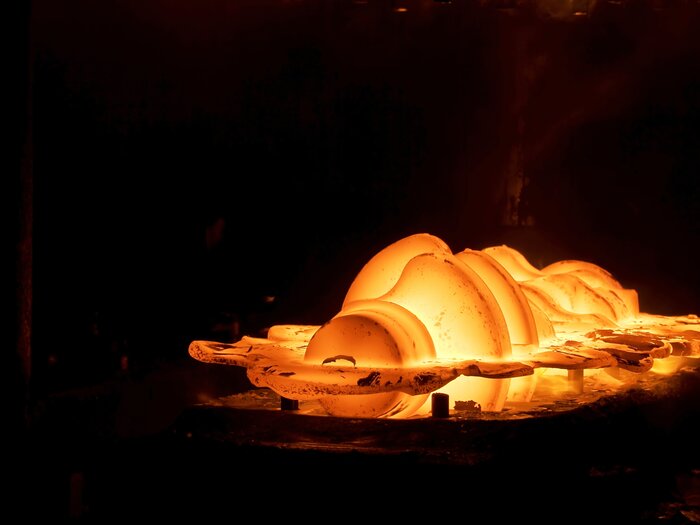
Due to previous processing steps such as rolling, bending, forging etc., quality reductions can occur in the workpiece. These can be reversed by annealing.
At RUBIG, various annealing processes are available to our customers in order to restore the desired properties of the workpieces.
The annealing processes can be carried out under protective gas or under vacuum. We offer our annealing processes for a wide variety of materials (e.g. steel, aluminum, titanium, copper alloys, nickel-based alloys, ...).
An overview of annealing processes
Stress relief annealing
Stress relief annealing is a special heat treatment under a protective gas atmosphere that reduces mechanical and thermal stresses (residual stresses) as well as solidifications without significantly changing the microstructure. Stress relief annealing is essential for components with difficult shapes and a risk of distortion as well as for complex geometries after rough machining.
The stress relief annealing temperature for most steels is in the range of 450°C to 650°C. The duration of the annealing treatment takes a few hours and depends on the annealing temperature and the size of the workpiece (cross section). In order to avoid new thermal stresses, it is important that the components are cooled slowly after the holding time.
In principle, stress relief annealing can be used for metallic materials such as aluminum alloys, copper, brass, titanium and titanium alloys. It can be executed according to customer-specific factory standards or according to the time-temperature specifications of the manufacturer.
Soft annealing and spheroidizing
Our soft annealing and spheroidizing processes are special heat treatments under a protective gas atmosphere, which are aimed at forming carbides and reducing hardness. This annealing treatment improves the machinability and (cold) formability of the workpieces and optimally prepares the structure for further heat treatments such as hardening.
The soft annealing temperature is usually between 650°C and 800°C, and the annealing treatment takes a few hours (2-4 hours on temperature). The exact duration depends on the annealing temperature and the size of the workpiece.
Normalizing
Normalizing (also known as normalizing annealing) is a special heat treatment under a protective gas atmosphere, which accomplishes a uniform structure with fine grain. This so-called "normalized" structure can either be an intermediate state before further thermal treatments such as hardening or the final state of use of the component with high strength and toughness.
Normalizing can help to reduce the rolling structure, reduce the tendency to brittle fracture, make the forging structure more uniform, eliminate the rough cast structure, improve strength and toughness and achieve uniform microstructure formation in the weld metal, the heat-affected zone, and in the base material.
In order to obtain the desired properties, an optimal coordination of the annealing treatment with our customers is of decisive importance. At RUBIG, normalizing is therefore only carried out after detailed coordination with our customers.
Solution annealing
Solution annealing, also known as homogenizing, is an important heat treatment for both austenitic steels and for duplex steels. The aim of this treatment is to evenly distribute carbide precipitations and other mixed crystal phases in the microstructure by bringing them into the solution. Subsequent rapid cooling prevents re-precipitation. This does not only improve the corrosion resistance, but also distributes the alloying elements in the material uniformly.
The high treatment temperature, typically in the range of 950°C to 1,200°C, makes it possible to correct and compensate for cold deformations caused by machining (e.g. deep drawing) or microstructure changes and stresses caused by thermal processes (e.g. welding) (recrystallization).
Remanence-free annealing (Magnetic final annealing)
Remanence-free annealing, also known as magnetic final annealing, is a specialized process in heat treatment that aims to eliminate the magnetic properties of steel and other metallic materials. This technique is particularly relevant for applications where magnetic remanence – the residual magnetization after removal of an external magnetic field – is undesirable. Through carefully controlled heating and cooling cycles, materials can be made remanence-free, which makes them ideal for use in electrical engineering, mechanical engineering and other industries where materials are needed without magnetic interference. Remanence-free annealing is therefore an essential process for ensuring the functionality and reliability of components in magnetically sensitive applications.
Other annealing treatments
Further annealing treatments such as diffusion annealing, FP annealing (BG annealing), recrystallization annealing, pearlite annealing, ferrite annealing are only offered after detailed consultation.
Individual process management can be carried out on customer inquiry.
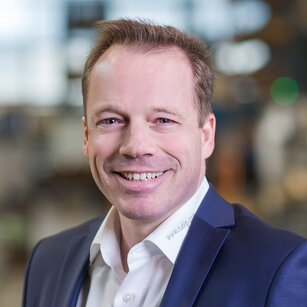
ANY QUESTIONS?
RUBIG Heat Treatment combines state-of-the-art technology and in-depth industry knowledge to optimise the finishing of your steel products.
DI David Unterberger
Head of Sales