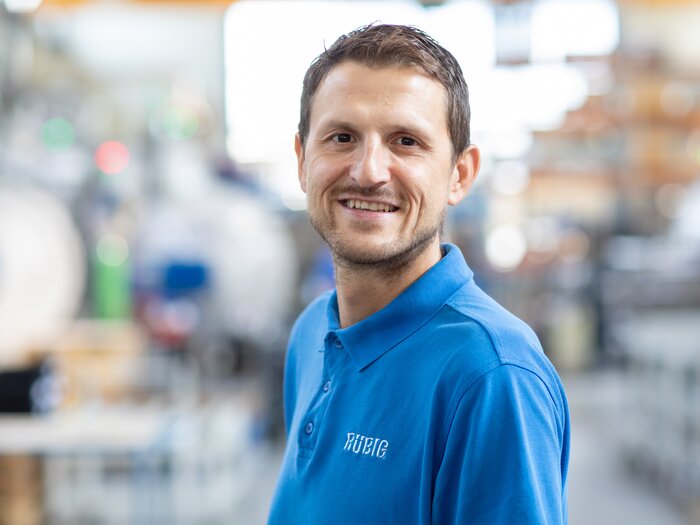
PACVD: Premium coatings for optimal protection of your components
Plasma assisted chemical vapor deposition (PACVD) uses plasma to enable chemical deposition. In conventional CVD processes the molecules of the reaction gas are broken up by heat, in PACVD they are broken up by accelerated electrons in the plasma. These create radicals and ions that cause the coating formation on the substrate. Thanks to this method, even temperature-sensitive materials can be coated, which is often not possible with conventional CVD processes.
RUBIG Hard coatings PLASTIT®
RUBIG offers PACVD coatings (PACVD - Plasma Assisted Chemical Vapor Deposition) under the name PLASTIT®. Thanks to the premium coatings, the surface of the component is optimally protected and service life is increased.
Plastit® process
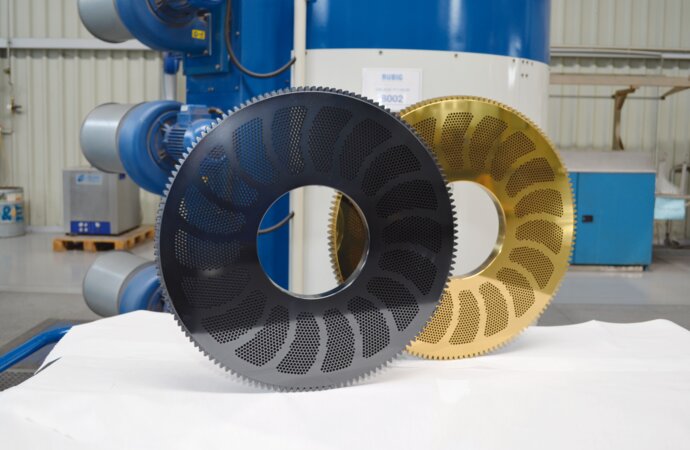
DLC Xtended® & DL coat (DLC)
Carbon-based coatings can have various properties, such as high hardness, wear resistance, corrosion resistance or electrical conductivity. They are often used in industry as a protective coating, wear protection or decorative coating.
A well-known example is the diamond coating, a carbon-based coating that is applied to tools or jewelry.
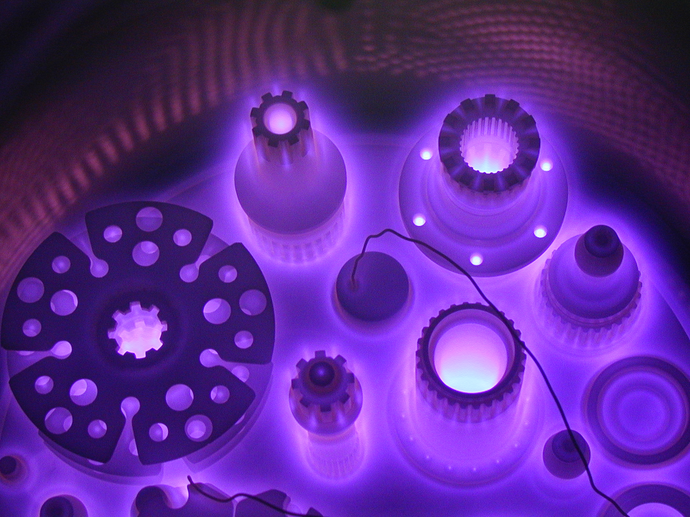
Carbon LF PLASTIT®& Gold LF PLASTIT® & BORON Nanocomp PLASTIT®
Titanium-based coatings are applied by various methods such as plasma spraying, electrolysis or chemical deposition and are mainly used to improve the corrosion resistance and wear resistance of titanium components.
Titanium-based coatings are particularly used in the aerospace, automotive and medical technology sectors.
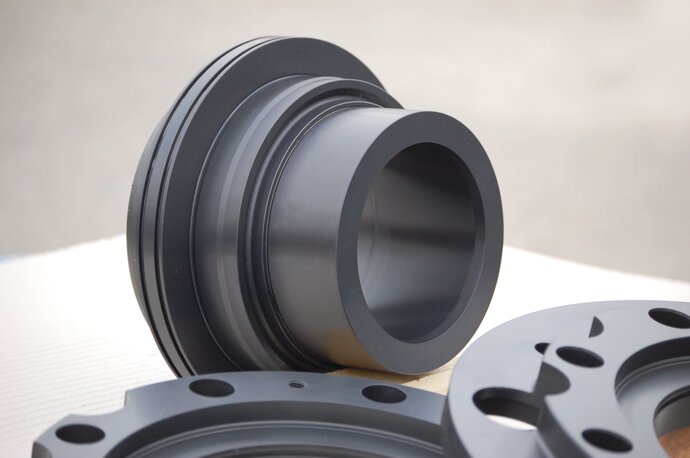
DUPLEX processes
RUBIG offers DUPLEX processes for all titanium-based coatings as well as for DLC Xtended® coatings.
DUPLEX means that both plasma nitriding and coating are carried out in one process. Nitriding the surface supports the hard coating and improves the adhesion of the coating.
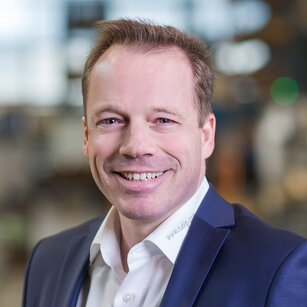
Maximum Protection for Your Components
PACVD delivers top-tier surface performance – and I’ll show you how to make the most of it. Let’s explore your options together!
DI David Unterberger
Head of Sales