Maximum usable furnace space: Ø 1,500 mm/6,000 mm height
Maximum batch weight: 10.000 kg
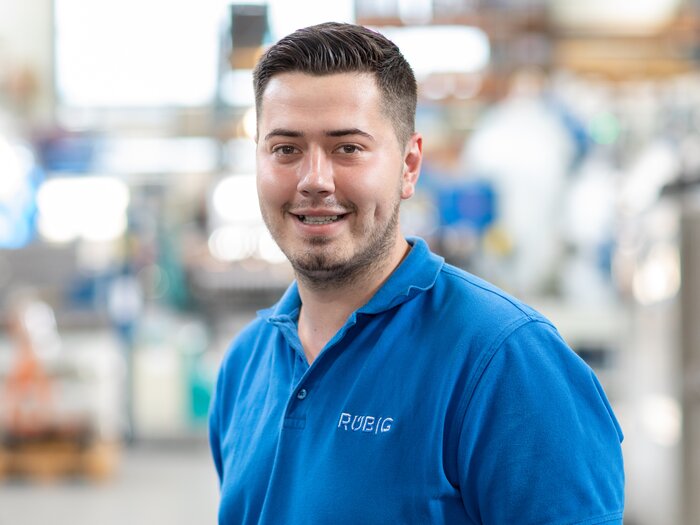
Plasma nitriding (PLASNIT®) has decisive advantages over gas or salt bath nitriding. Since plasma nitration usually takes place at lower treatment temperatures, it is the heat treatment with the comparatively smallest dimensional change. The great variability of the process control makes it possible to respond optimally to steel properties, customer requirements and, if necessary, restrictions due to the respective pretreatment. Nitriding hardness depth, surface hardness and joint coating thickness can be easily adjusted over a wide range of steels. Through targeted post-oxidation, an oxide layer is embedded in the compound layer, which improves the sliding properties and significantly increases the corrosion protection.
Components and tools with a plasma nitrided surface show improved wear resistance, better friction and sliding properties and higher fatigue strength. Because of the comparatively small dimensional change, finished machined parts are usually plasma nitrided. The so-called nitriding steels (e.g. 1.8519) are ideal for plasma nitriding.
PROCEDURE
Best-practice example of plasma nitriding
We offer customers highly developed plasma nitriding heat treatments for a wide range of steel grades. With our standard processes, we cover the recommended range of nitriding hardness depth and compound layer thickness for all common steels that can be heat treated by nitriding. A list of the most common steels/materials and their achievable values in our standard processes can be found under "typical plasma nitriding results".
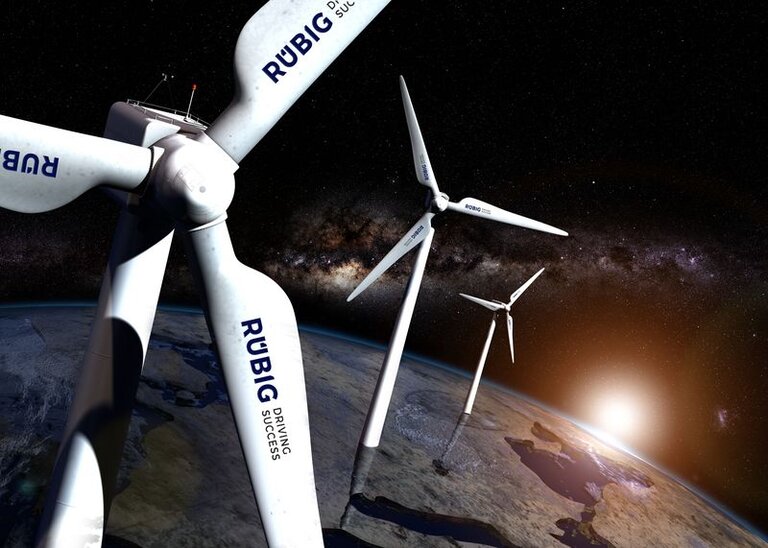
PLASMA NITRIDING IN WIND TURBINES
One of our satisfied customers for plasma nitriding systems is ZF Windkraft, a worldwide supplier of components for wind turbines. Around 25% of all wind turbines are equipped with a ZF transmission, the components of which are plasma nitrided using RUBIG technology.
The development of a new product was crucial in analyzing the existing production steps in more detail. Consequently, the necessary heat treatment steps were also evaluated and plasma nitriding was selected as the preferred heat treatment technology. This process was convincing due to its environmental friendliness and the process duration. The resulting task for the system supplier was to develop a plasma nitriding furnace for ring gears with a diameter of up to 3 m and to install it in Tianjin, China.
Tailor-made solution
RUBIG designed a plasma nitriding furnace with a usable diameter and a usable height of 3 m each. Lifting, handling and cooling systems had to be completely redesigned for these impressive dimensions. In addition, RUBIG established a new service location including a spare parts warehouse in Taicang, China, in order to provide the best possible support to the customer on site.
We build plasma nitriding FURNACES
Our strength is the individual development of plasma nitriding processes to meet your requirements in terms of nitriding hardness depth, compound layer thickness, corrosion protection and oxide layer thickness - for individual parts up to large series. Not only can you have your components plasma nitrided by us, we also build the corresponding plasma nitriding furnaces.
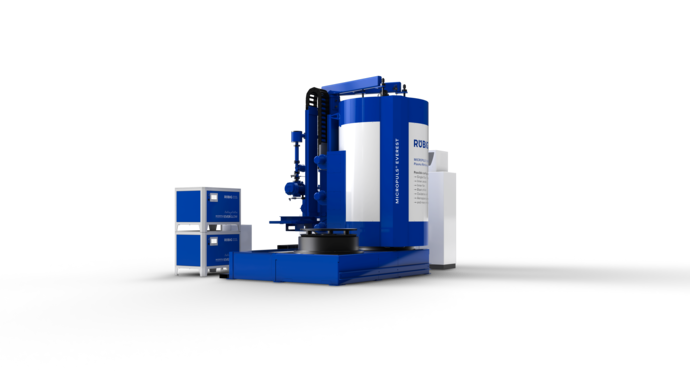
EVEREST
The plasma nitriding system MICROPULS® Everest offers our customers the cutting edge technology of nitriding . It is used in numerous industries, from automotive and contract heat treatment to aviation and wind energy.
TECHNICAL INFORMATION
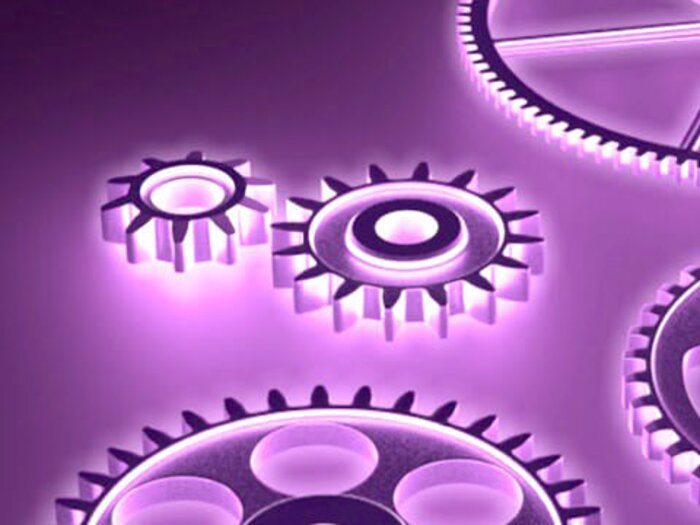
Suitable for:
Mechanical engineering, automotive, tool making, aerospace
Material:
- Structural steels (e.g. S355), low-alloy heat-treatable steels (e.g. 1.7225) and nitriding steels (e.g. 1.8519, 1.8550), tool steels
- (e.g. 1.2343, 1.2379) and plastic mold steels (e.g. 1.2311)
- Corrosion-resistant steels on inquiry
Possible surface preparation for an optimal surface condition:
- Metallic, bare surface
- No corrosion
- Microblasting
- Free of fats, oils, processing agents or drawn and cast skins
- Polishing
- Heating
- Clean cooling channels
- No work hardening by e.g. mechanical manufacturing
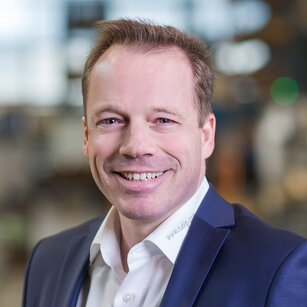
ANY QUESTIONS?
RUBIG Heat Treatment combines state-of-the-art technology and in-depth industry knowledge to optimise the finishing of your steel products.
DI David Unterberger
Head of Sales