Maximum oven usable space: Ø 1.500 mm / 2.400 mm height
Maximum batch weight: 7.500 kg
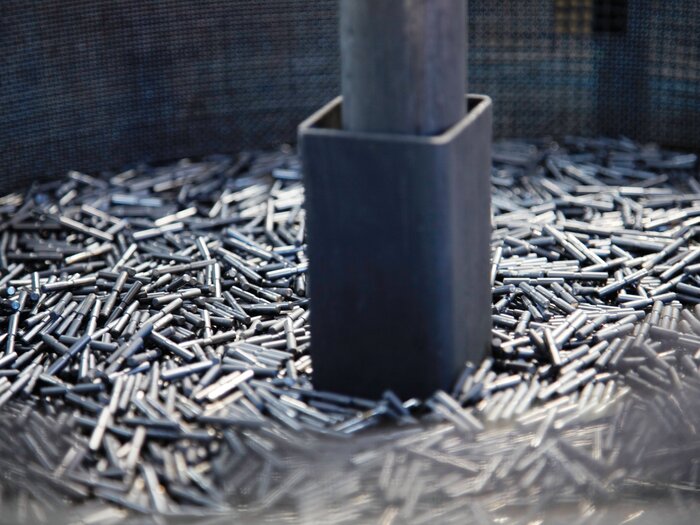
If a nitriding coating alone does not meet the requirements, subsequent oxidation (directly in the nitriding process or as a separate process) can further improve corrosion resistance and coefficient of friction. In the targeted post-oxidation, an oxidizing atmosphere (e.g. by adding H2O or O2) the iron nitride coating on the surface of the workpiece is converted into an iron oxide layer.
The appropriate choice of temperature (up to 600°C), time and atmosphere can increase the corrosion resistance of a nitriding coating by a factor of 10. The surface of oxidized workpieces is anthracite-colored and has a lower coefficient of friction than nitrided surfaces.
- Material
- Surface hardness
- Nitriding hardness depth
- Compound layer thickness
- Possible pre-treatments
- Oxide layer thickness
- Possible coverage areas
- Do areas need to be protected from nitriding? (Cover)
Classic applications
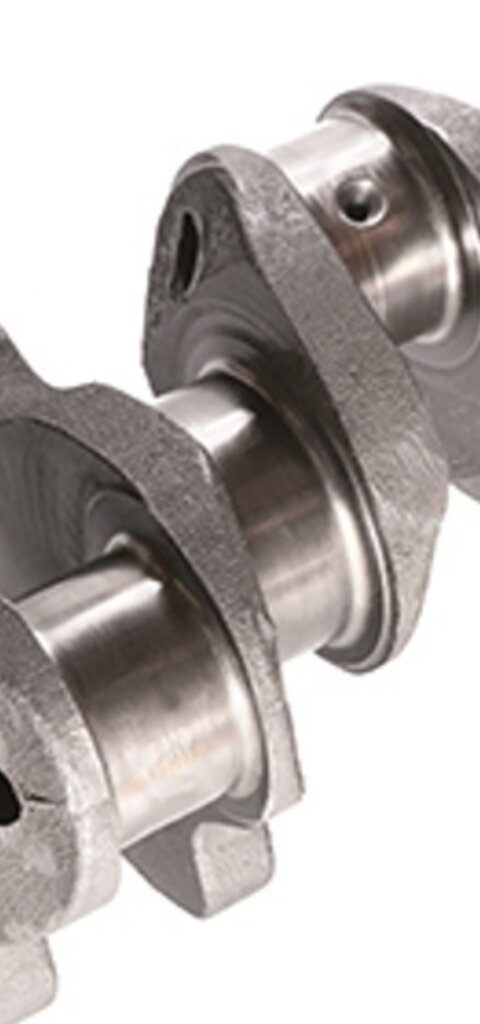
Crankshafts, camshafts, toothed shafts, connecting rods ...

Gears, ring gears, pinions, ...
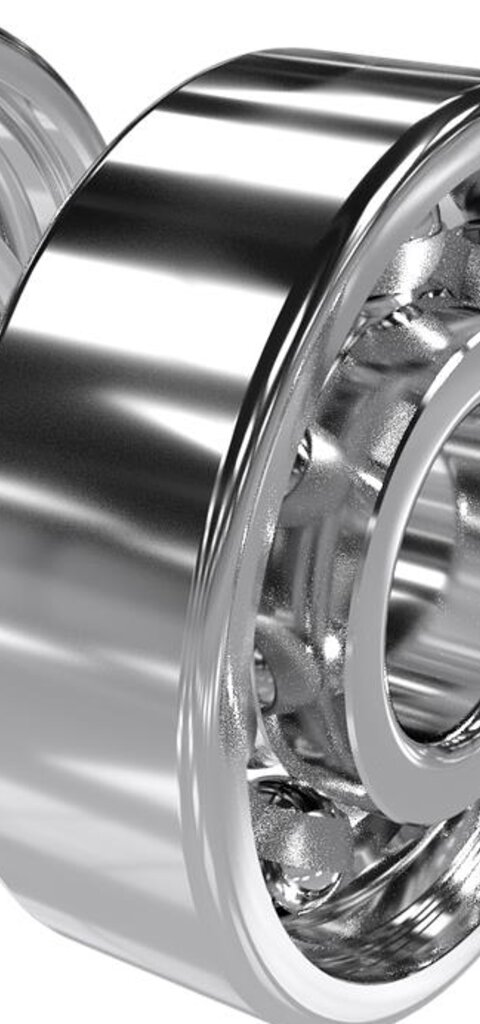
Bearing rings, bearing balls, ...
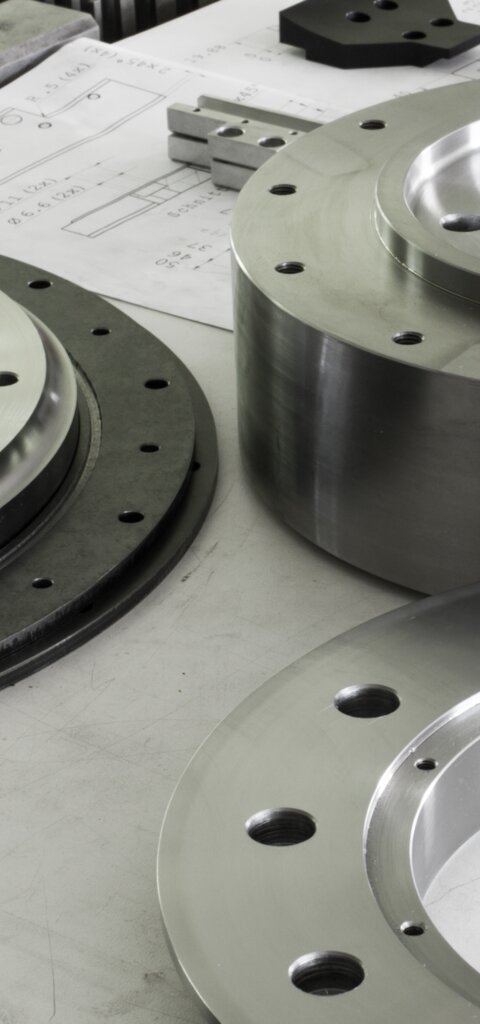
Machine tool parts
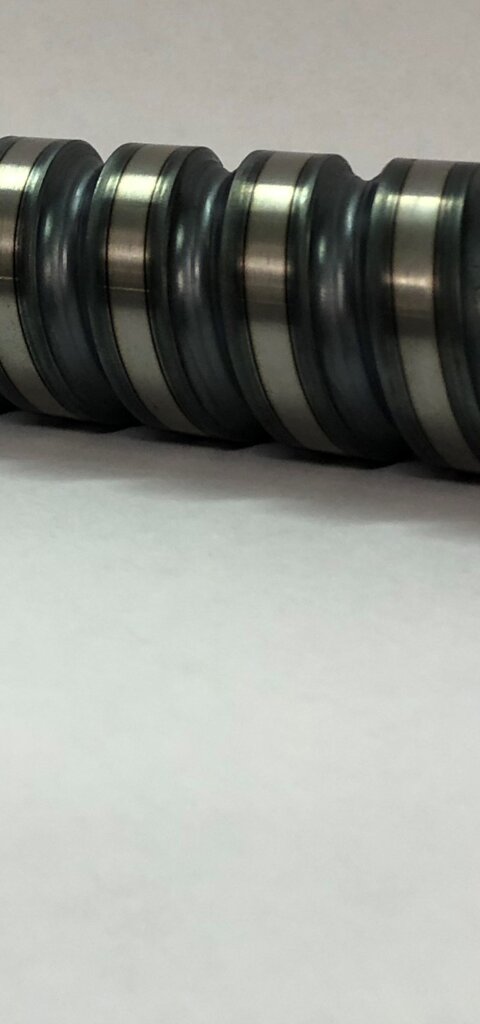
Spindles and screws
Our gas nitriding system
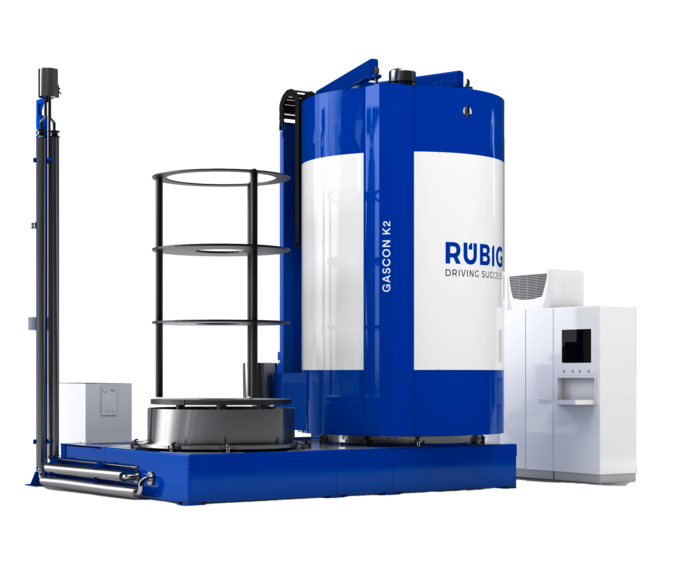
GASCON K2
RUBIG's gas nitriding systems are the result of decades of experience and further developments. RUBIG Industrial Furnaces' GASCON Technology stands for highly efficient and advanced gas nitriding.
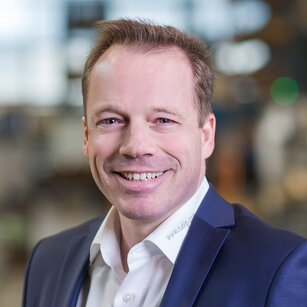
ANY QUESTIONS?
RUBIG Heat Treatment combines state-of-the-art technology and in-depth industry knowledge to optimise the finishing of your steel products.
DI David Unterberger
Head of Sales