Maximum usable furnace space: 1.520 x 1.200 x 1.045 mm (L x W x H)
Maximum batch weight: 2.300kg
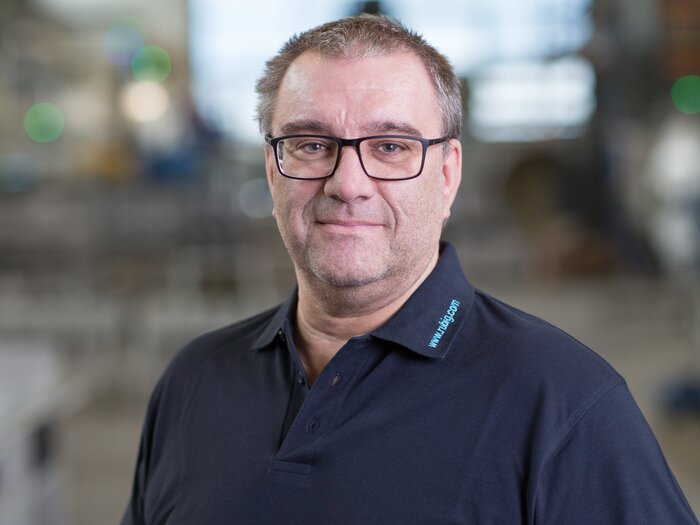
Case hardening is one of the most traditional thermochemical heat treatment processes. In close cooperation with our customers, components can be optimized for maximum dimensional accuracy and the tightest tolerances.
Not all case hardening processes are the same. Under R.CARB+® you will find RUBIG's various case hardening processes. Tight tolerances and the highest reproducibility are a matter of course. RUBIG's R.CARB+® processes are also characterized by hardness and dimensional stability.
Workpieces treated with R.CARB+® have increased fatigue strength, improved wear resistance and a combination of a hard, wear-resistant edge and a tough core. The method is particularly suitable for transmission parts, gears, shafts etc.
R.Carb+® process overview
Case hardening
Case hardening is a combination of carburizing and hardening process including tempering. In the process, a carburized edge region with a carbon content of 0.6 - 0.8% is formed, which decreases continuously towards the core. After the hardening process, an edge with high hardness and a soft, tough core is formed. Insert steels with carbon contents below 0.25% by mass are suitable for the carburizing process.
Benefits:
- Increased fatigue strength
- Increased wear resistance
- Combination of hard, wear-resistant edge and tough core
Inert gas hardening
In this hardening process, the components (e.g. tools) are protected in a reactive atmosphere from a negative influence on the edge zone (e.g. decarburizing). Quenching is carried out during inert gas hardening in an oil bath and as a result even unalloyed and low-alloyed steels can be hardened. Through further treatments, strength, toughness, wear resistance and other properties can be adjusted over a wide range.
Inert gas hardening is suitable for quenched and tempered steels (e.g. 1.7225), ball bearing steel (e.g. 1.3505) and carbon steels (e.g. C45)
Benefits:
- Improvement of physical component properties
Carbonitriding
During carbonitriding, the edge zone of a component is enriched not only with carbon, but also with nitrogen. This improves the hardenability, which makes it possible to treat even unalloyed steels (structural steels). Similar to case hardening, a hard and wear-resistant edge area with high strength is created, while the core of the component remains tough.
This method is particularly suitable for certain components such as transmission parts (ring gears, spur gears), crankshafts and drive shafts. A special variant of this process is the High carb process, which leads to improved tempering resistance and hardenability due to special process control. This makes the components particularly resistant and durable.
Benefits:
- Also suitable for unalloyed steels
High Carb
High carb is a special variant of carbonitriding and leads to improved hardenability and tempering resistance.
Application area:
- For adjusting the strength and toughness properties for special component geometries with very high requirements
- Increase of wear protection and fatigue strength characteristics
- Increasing the application temperature of case-hardened components
Suitable for:
- Tool making
- Automotive
- Aerospace
Carburizing
When carburizing, the outer coating of a steel, usually insert steels, is enriched with carbon. Subsequently, a slow cooling takes place under a protective gas atmosphere, so as not to produce any additional hardness. As a result, the components can be processed before the actual hardening process takes place. A great advantage of this method is that no additional reworking is required due to the cover.
Materials that are suitable for the carburizing process have carbon contents of less than 0.25 percent by mass and are often case-hardened steels.
Suitable for:
- Tool and mechanical engineering
- Automotive
- Agricultural machines
- Aerospace
Tempering
Tempering is a special combination of hardening processes (such as vacuum or inert gas hardening) and subsequent tempering at high temperature. This process is also often abbreviated as "QT" (quenched and tempered).
Tempering treatment is carried out at high temperatures up to 700°C in order to achieve an optimal balance of strength and toughness. Therefore, tempering is particularly important and useful for components that are exposed to dynamic loads, e.g. shafts.
Suitable materials:
- Tempered steels
Nitriding steels
Tool steels (cold, hot and high-speed steels)
Benefits:
Good combination of toughness and strength
Deep freezing
Deep freezing is usually carried out at temperatures down to -120°C and lasts for several hours. An additional variant is the so-called cryotreatment or cryotherapy. In this process, the temperature is even lowered to -196°C and the time on temperature goes far beyond the usual warm-up time.
Deep freezing is always useful or necessary when components have to meet the following requirements:
High wear resistance:
As a result of deep freezing, the residual austenite is converted into martensite, which leads to an increase in hardness.
Dimensional and form stability:
The deep freezing process results in a stable and homogeneous structure that shows little or no changes during use.
Tempering
During tempering, steel is heated to a low temperature in order to specifically adjust properties such as hardness and toughness. As a rule, the tempering is intended to relieve stresses that have been built up by previous hardening of the material.
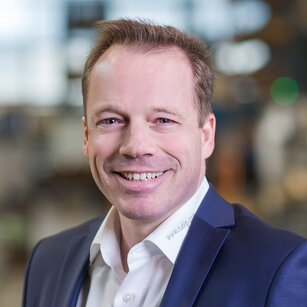
ANY QUESTIONS?
RUBIG Heat Treatment combines state-of-the-art technology and in-depth industry knowledge to optimise the finishing of your steel products.
DI David Unterberger
Head of Sales – Heat Treatment