Every component, tool or welded construction is under residual stress. Even primary materials are not free from stress. Residual stresses are stresses in a closed system on which no external forces or moments act. The residual stresses equalize over the cross-section of a component, so residual tensile and compressive stresses always occur together.
Residual stress measurement
23.11.2021
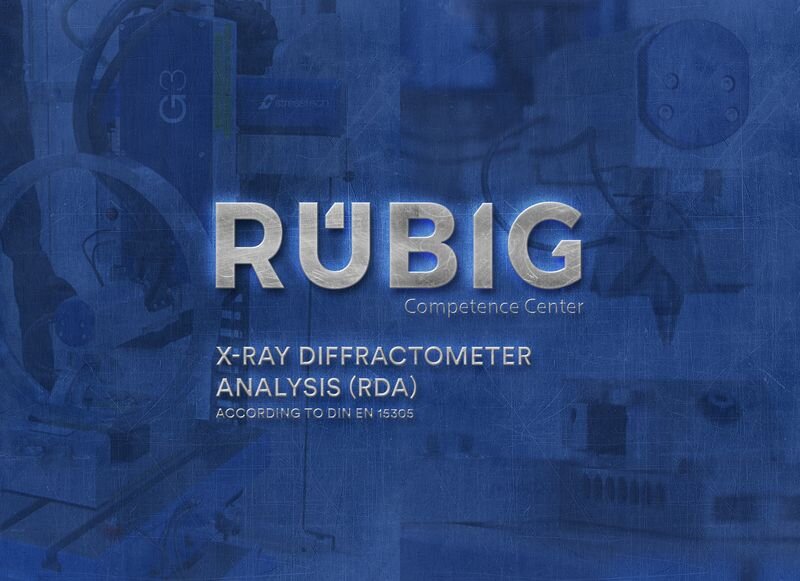
RUBIG can measure the residual stresses of your workpiece. Especially in the case of component optimizations that are aimed at increasing the fatigue strength, or in the case of fatigue strength calculations and fatigue tests, etc., the knowledge of the level and the course of the residual stresses is very crucial.
The most reliable and accurate method for residual stress measurement is X-ray diffractometer analysis (RDA) according to DIN EN 15305.
The following must be observed:
- Due to the design of the RDA, not only small samples but also larger components can be tested
- Small test areas (Ø 0.3 to 5 mm) measurable
- Residual stress curves: The measurement of the residual stresses gains in significance when a depth curve is recorded. For this purpose, the material is removed electrochemically in the component edge zone, during this process no further mechanical stresses are introduced that could falsify the result.