Cut Costs in the Aluminum Extrusion Process
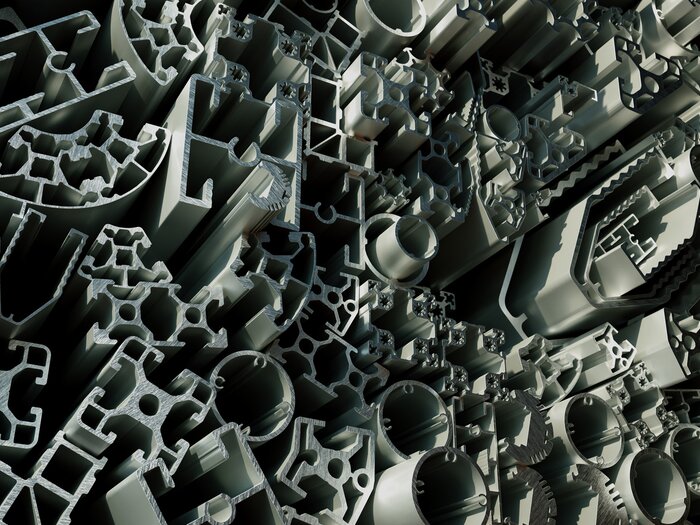
Aluminum extrusion is a highly precise manufacturing process where aluminum alloys are pressed through specialized tools (dies and mandrels) under specific conditions to create complex profiles with minimal weight. Due to their low density, corrosion resistance, and excellent formability, these aluminum profiles are essential components in industries such as automotive, mechanical engineering, electrical engineering, and aerospace.
Key to Efficiency: Press Speed and Exit Speed
A critical factor in tool manufacturing for aluminum extrusion is the optimal adjustment of press speed and exit speed (measured in meters per second, m/s). Both parameters significantly influence profile quality and the lifespan of extrusion tools.
While high exit speeds can temporarily boost production output, they often lead to increased tool wear, unwanted material adhesion, and reduced tool life. Surface treatments of extrusion tools specifically address these issues, achieving an ideal balance between high speed and maximum tool longevity.
Those who strategically optimize press and exit speeds can cut costs in the aluminum extrusion process—without compromising on quality or tool life.
Nitriding – Extended Tool Life and Enhanced Process Reliability
"Through targeted nitriding, we significantly extend tool lifespans. This allows our customers to achieve higher pressing speeds while simultaneously reducing production downtime - a crucial competitive advantage," explains Stefan Haas, Sales Director at RUBIG Industrial Furnaces.
The benefits of nitriding at a glance:
- Enhanced Wear Resistance: Nitrogen penetration creates a robust protective layer on the tool surface, substantially extending its lifespan.
- Reduced Aluminum Adhesion: The optimised surface minimises material adhesion, enhancing process stability and allowing consistently high exit speeds.
- Improved Corrosion Resistance: The nitrided layer effectively protects against chemical reactions between tool surfaces and aluminum.
- Enhanced Process Reliability and Quality: Tools retain their precise shape for longer, ensuring consistently high product quality.
Hot Work Steels for Maximum Performance
Typical materials used in aluminum extrusion tool manufacturing are high-strength hot work steels such as H13 (1.2344), H11 (1.2343), or 1.2367, designed to optimally withstand thermal and mechanical stresses. Nitrided hot work steels exhibit excellent resistance to abrasion, thermal fatigue, and corrosion, significantly improving tool life and cost efficiency.
RUBIG Sets Standards with Gas and Plasma Nitriding. RUBIG offers innovative gas and plasma nitriding processes, which are specifically tailored for aluminum extrusion.
- Gas Nitriding: This process ensures uniform surface hardening with excellent penetration depth and homogeneity, making it ideal for highly stressed tools.
- Plasma Nitriding: This environmentally friendly and energy-efficient process retains all the technological advantages of gas nitriding.
Conclusion: Sustainably Faster and More Economical
Through targeted nitriding processes by RUBIG, tool manufacturers and extrusion operators achieve an optimal combination of increased press and exit speeds, extended tool lifespans, and consistently high aluminum profile quality. This optimization not only facilitates sustainable cost savings but also strengthens market competitiveness over the long term.
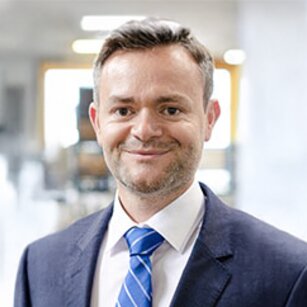
Innovative and Tailor-Made
With over three decades of technology leadership, we develop a system concept precisely tailored to your manufacturing processes. Speak with our expert to implement a solution that sustainably optimizes your production.
DI Stefan Haas
Head of Sales