Plasma Nitriding for Increased Service Life of Thread Rolling Tools
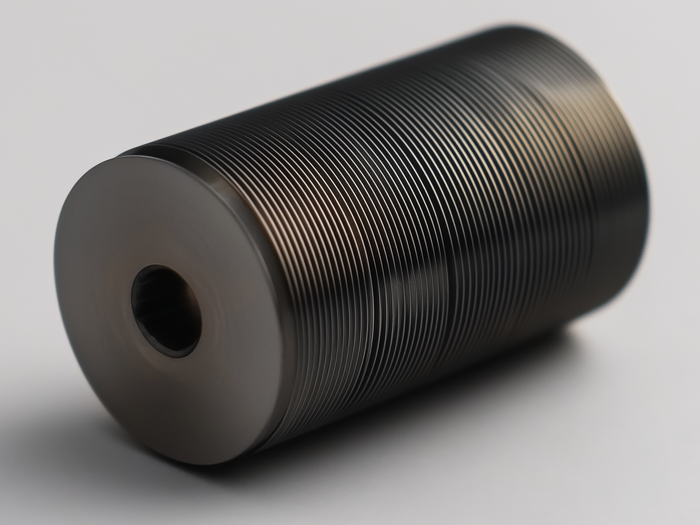
Thread rolling tools must make a lasting impression – literally. Their function is to form threads on screws, bolts and other cylindrical workpieces with great precision. This is achieved through a cold forming process, in which the workpiece is rolled between hardened tool dies. It is therefore essential to protect these tools against wear as effectively as possible. Plasma nitriding of thread rolling tools is a proven solution that ensures their durability and reliability in the face of constant use.
Why Surface Hardening Is Crucial for Thread Rolling Tools
Wear mechanisms such as abrasion, galling, or oxidation can cause significant stress to the tools. Without targeted surface treatment, tool life is drastically reduced. Despite the fact that thread rolling tools are frequently manufactured from high-alloy tool steels (such as HSS, PM, or cold work steels), their low tempering temperatures restrict the application of conventional heat treatment methods.
The solution: Plasma nitriding is a precise, gentle and effective solution.
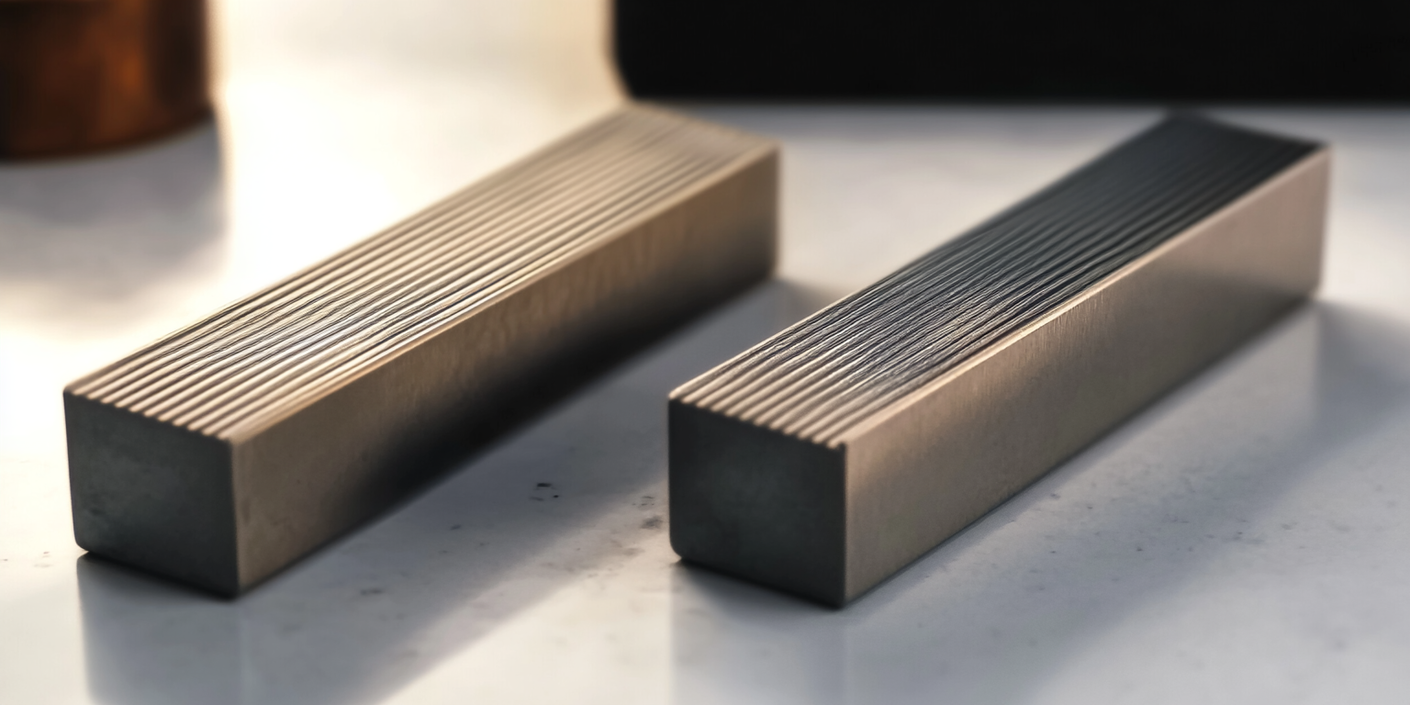
Overview of the Process
Plasma nitriding is a thermochemical process in which nitrogen is diffused into the surface of the tool. This process occurs within a vacuum chamber filled with ionised gas (plasma). The result is a tool with enhanced durability and improved performance. This process creates a hard, wear-resistant nitrided layer, making it ideal for use in thread rolling tools.
Advantages of Plasma Nitriding:
- Extended Tool Life and Cost Efficiency
The surface hardness of the product has been significantly increased while abrasion has been reduced. This increases the service life of thread rolling tools by up to 50% while simultaneously lowering unit costs. - High Toughness Despite Hardness
Even under cyclic loading or the presence of microcracks, the tool remains resistant to failure – making it ideal for the dynamic rolling process. - Minimal distortion – excellent dimensional stability
Unlike conventional hardening methods, the tool's shape remains virtually unchanged – ensuring precision in thread production. - Nitriding Without Compound Layer
Plasma nitriding enables a compound layer-free hardening process, preventing crack formation and chipping. This significantly increases the durability of thread rolling tools and enhances their resistance to wear during demanding rolling operations. - Sustainable Process
The process does not involve the use of toxic gases or chemical baths. This makes plasma nitriding one of the most environmentally friendly surface treatment methods in heat treatment technology.
Conclusion:
RUBIG has decades of experience in heat treatment and supports companies worldwide in optimising their rolling processes. Plasma nitriding of thread rolling tools provides exceptional wear resistance, as well as a measurable increase in efficiency and a reduction in manufacturing costs. Choose long-lasting tools – choose plasma nitriding.
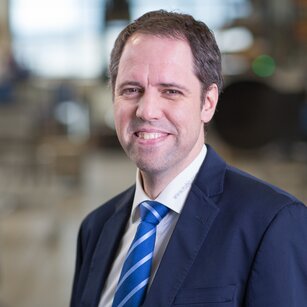
Superior Surface Quality Through Plasma Nitriding
Achieve optimal results in dimensional accuracy, friction resistance, and corrosion protection: RUBIG plasma nitriding delivers wear- and corrosion-resistant surfaces, making it ideal for demanding applications in the automotive, mechanical engineering, and tooling industries.
If you have any questions, please do not hesitate to get in touch.
Martin Strutzenberger MSc
Sales Manager