PECVD / PACVD
Coating:
DLcoat PLASTIT® and DLC Xtended®
RÜBIG offers two main variants in the field of carbon-based coatings to meet diverse requirements: DLcoat PLASTIT® as a standard low-temperature DLC coating and DLC Xtended® as an advanced DLC layer that also serves as a hard chrome alternative. Both processes are based on PACVD (Plasma-Assisted Chemical Vapor Deposition) and deliver hard, wear-resistant layers, differing in process execution and application profiles.
A significant advantage of RÜBIG's PECVD / PACVD technology is its flexibility concerning component geometry. Unlike purely line-of-sight dependent processes (e.g., PVD), PACVD can uniformly coat complex shapes and internal contours.
PACVD allows even internal bores from approximately 5 mm in diameter to be lined with DLC. (Only the ratio of bore diameter to length needs to be considered—very deep, narrow channels have limited coatability, as the layer thickness decreases with depth.)
RÜBIG has experience with internal coatings where the deposition rate inside can even be higher than outside. This opens up possibilities to protect the interiors of pipes, cylinders, or hollow shafts against wear and corrosion—applications that are not feasible with many other processes.
Regarding component size, RÜBIG is well-equipped: the largest PACVD system accommodates parts up to Ø 1.4 m and 2 m in height. This enables even large rollers, cylinder tubes, or molds to be coated in one piece. For very small components, the specialized DLcoat system is available, optimized for small and precision parts.
Coatable Materials: DLC coatings are mainly used on metal substrates. They’re especially well-suited for hardened steels, tool steels, and commonly used case-hardening or nitriding steels. When needed, these materials can be nitrided directly during the DLC Xtended process. Stainless steels can also be coated, though pre-treatment with plasma nitriding is often recommended to improve surface hardness.
Aluminum and other non-ferrous metals can be coated too, but only using the pure DLC process (DLcoat) at low temperatures, since they can’t withstand the heat involved in duplex treatments. It’s also important to ensure that the base material has sufficient tempering resistance if a high-temperature duplex process (450–500 °C) is being considered.
Surface Condition and Pre-Treatment
To achieve optimal coating results, the component surface should be metallically clean and as smooth as possible. RÜBIG recommends polishing or fine grinding before coating, as the roughness is only slightly reduced by the DLC layer, and the coating tends to replicate the surface texture. Typically, roughness slightly increases due to application of the coating. Furthermore, surfaces must be free from corrosion, fats, and residues. As an optional pre-treatment, RÜBIG can perform micro-blasting to promote adhesion. If necessary, plasma nitriding is also carried out before coating (either as a separate step or integrated into the duplex process). PECVD / PACVD offers a key advantage: no post-processing is needed—the coating is ready to use straight from the system. There are no splatters or droplets that need to be laboriously removed, and dimensions remain within tight tolerances.
PACVD with
DL coat PLASTIT®
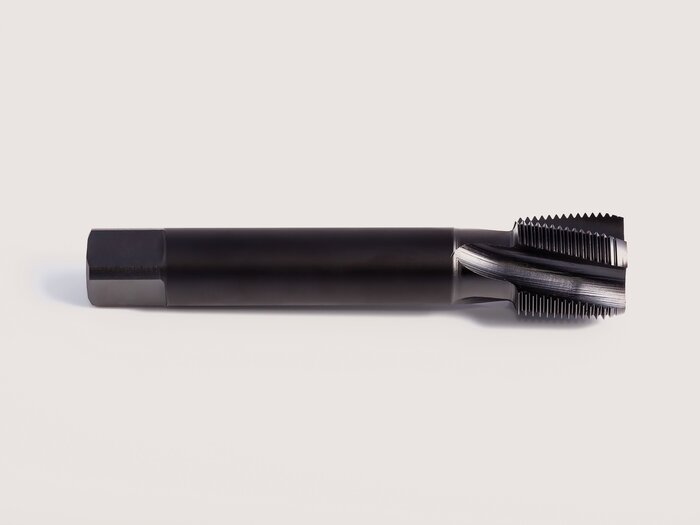
DL coat PLASTIT® is a DLC (Diamond-Like Carbon) coating applied at approximately 150–200 °C specifically developed for temperature-sensitive components and smaller parts. Typical characteristics of this coating include a layer thickness of around 2 µm and a hardness ranging from approximately 2000 HV up to 3500 HV. The coating color is anthracite, and the surface is very smooth and virtually free of particles or droplets, as the PECVD / PACVD process ensures uniform layer growth. DLC coatings are also used in plastic injection molding technology or for ejectors, sliders, and components that, for production-related reasons, cannot receive lubrication.
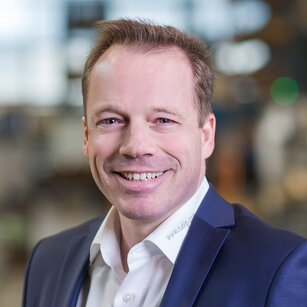
Need Help with PECVD / PACVD Coatings?
DLC offers top-tier surface performance – and I’ll show you how to benefit from it. Let’s explore your options together!
DI David Unterberger
Head of Sales
Where is DL coat PLASTIT® suitable?
Primarily for components that require solid base wear protection and friction reduction, but do not demand extremely thick coatings. Examples include plastic injection molds, precision parts, valves, or sliding machine elements that have been tempered at manufacturing temperatures below 200 °C. Aluminum parts can also be coated with DLcoat.
The coating significantly increases the service life of these components without dimensional changes (DLC ~2 µm thin) and without the need for post-polishing. DLcoat layers are also used decoratively, for example, when a uniform anthracite-colored appearance is desired.
Note: Due to the smaller DLcoat system, components up to a maximum size of approximately 100 × 200 × 400 mm can be coated. For larger parts or greater coating thicknesses, DLC Xtended® is used.
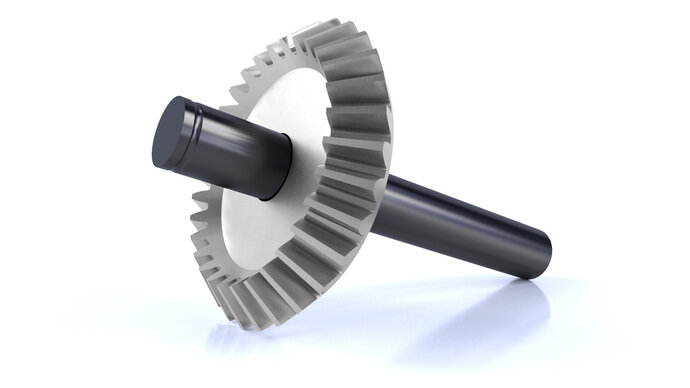
PACVD with
DLC Xtended®
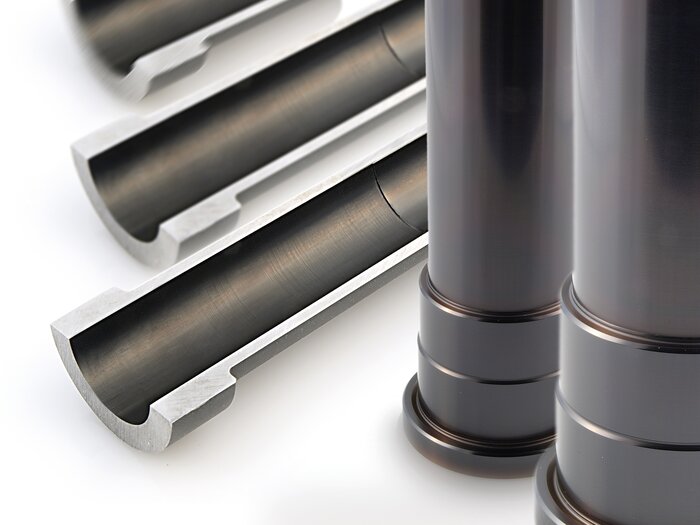
DLC Xtended® refers to a DLC coating developed by RÜBIG that can optionally be applied in combination with plasma nitriding (duplex process).
This method allows for greater coating thicknesses and improves the bonding of the hard DLC layer to the base material through a gradual hardness transition zone (avoiding the "eggshell" effect of a brittle surface layer). A thin diffusion zone (~0.1–0.2 mm) in the steel ensures anchoring and additional hardness at the edge. In addition, RÜBIG always deposits a silicon-containing interlayer (a-C:H:Si) at the coating/substrate interface, which provides excellent adhesion of the DLC layer.
DLC Xtended® is typically applied at temperatures around 400–500 °C. Therefore, this process is particularly suitable for steels with sufficiently high tempering resistance (> 480 °C). If required, DLC Xtended can also be applied without prior nitriding.
In this case, the process temperature remains lower (~450 °C for the DLC deposition), and only the DLC layer (with silicon bonding) is applied. Depending on the material and requirements, RÜBIG can flexibly decide whether a duplex process (nitriding + DLC) or only DLC is the appropriate choice.
Thanks to the unique combination of MICROPULS® plasma nitriding and hard coating, surface hardnesses of 500 to 2500 HV can be achieved.
With specially developed process parameters, through-holes with a diameter-to-length ratio of 1:15 can be coated (minimum diameter > 15 mm). For this innovation, RÜBIG received the "Prix de l'Innovation" in France.
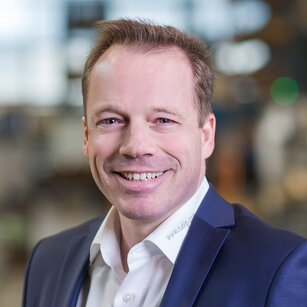
HOW CAN I HELP?
DLC delivers top-level surface performance – and I’ll show you how you can benefit from it.
Let’s explore your options together!
DI David Unterberger
Head of Sales
PACVD by coating type
"Hard" Coatings
Maximum coating hardness of approximately 2500 HV for highest wear protection.
"Soft" Coatings
Slightly lower hardness range (minimum hardness from 500 HV) to allow greater adaptability to the counter body. This tougher DLC coating can be advantageous when a certain “compliance” of the coating is desired in case of deformation or impact loading.
"Thick" Coatings
While standard DLC is typically 1–3 µm thin, DLC Xtended® coatings can be built up significantly thicker. Common thicknesses are 5–15 µm; in special cases, even 20–30 µm coating thicknesses are possible. Such thick coatings offer increased corrosion protection and longer service life, as more coating volume is available to resist wear.
Run-in Layer
To further optimize friction behavior—especially during the run-in phase and in frequent start-stop cycles—RÜBIG has developed a thin run-in layer. In this process, a soft top layer about 0.5 µm thick with slightly modified chemistry is applied on top of the hard DLC.
This layer wears off during the run-in phase and adapts to the counter surface. The result is significantly improved run-in behavior and further reduced friction in continuous operation (coefficient of friction reduced to ~0.03). After that, the underlying hard DLC layer continues to perform.
Hard Chrome
DLC Xtended® is the ideal solution as a replacement for hard chrome on highly stressed components. Typical applications include hydraulic cylinder rods, pistons, and components in mechanical and plant engineering that were previously hard-chrome plated.
DLC Xtended® is also used in the automotive industry (e.g. engine parts, valve drives, or injection components) and in tool and mold making, where both wear resistance and corrosion protection are required. Thanks to duplex technology, the typical requirements for hard chrome coatings are met or even exceeded — while also offering improved environmental performance (no Chromium VI).
Our Dlc coating system
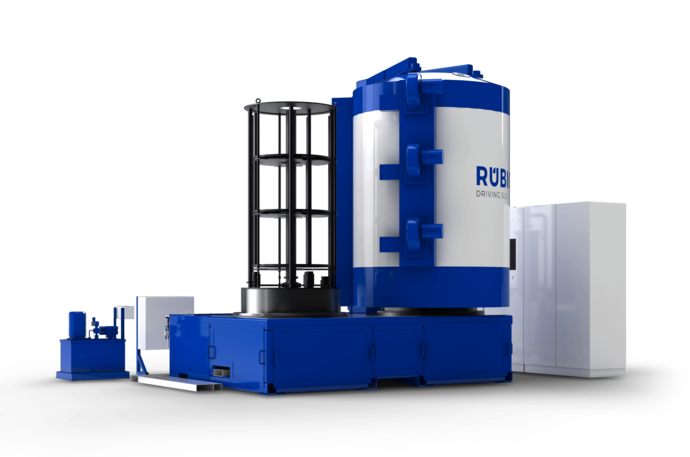
Diamond Xtended
With the MICROPULS® Diamond Xtended RUBIG supplies one of the most innovative system solutions in the field of DLC coating technology.