Perfectly designed and carefully planned, but failed in practice: the strengths and weaknesses of a component often only become apparent during real use. As a consequence of this setback, companies have to start the development process anew. This costs time and money. Both are resources that are only available to a limited extent. In order to avoid failures, we advise bringing experts on board from the very beginning.
We are here for you in case of damage: We optimize your product
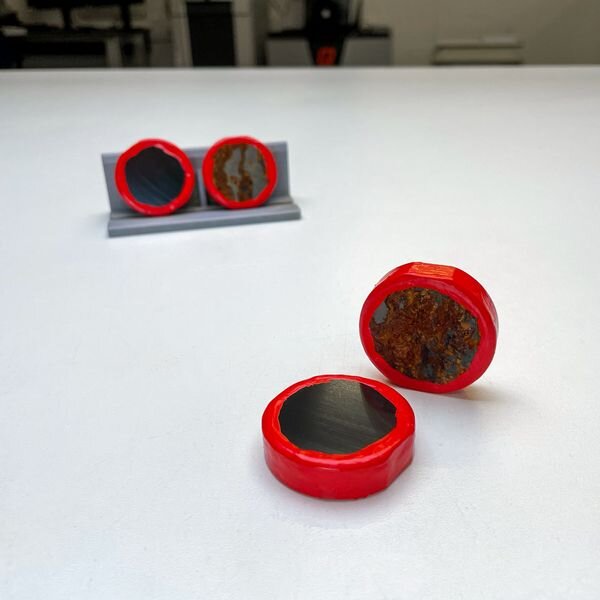
Your expert for steel
RUBIG is an expert in steel and has been working with this material for over 70 years. This wealth of experience and comprehensive know-how benefits our customers. In the event of damage, the experts are also commissioned with investigations into materials.
We accompany you: Process development using the example of corrosion
One problem that many customers face is corrosion. Due to the effects of corrosion, costs of about 3-4% of gross domestic product are incurred in industrialized countries. Whether a steel corrodes depends on various factors, such as the interaction between material composition, heat treatment condition, coatings used and environmental conditions.
From defective to mass-produced components
In the first step, the RUBIG experts assess the initial condition, which led to corrosion damage. Subsequently, various tests provide information about the cause of corrosion. Among other things experts use the neutral salt spray test, current density/potential measurement and impedance spectroscopy. In addition, a combination of corrosion and wear can be tested with the help of tribocorrosion measurements. By means of the test results, the experts can derive suitable and practicable prevention measures. This can be, for example, a special hardening process or a specific coating. In the next step, corrosion tests are carried out again on the modified component and the corrosion resistance is determined. At the end, the customer receives a corrosion-resistant component that is ready for series production.
Worth knowing: An untreated unalloyed or low-alloy steel will rust in the neutral salt spray test after only one to two hours. A steel treated by RUBIG, e.g. with Duplex DLC Xtended® coated, withstands this spray mist test for up to 1000 hours and longer.